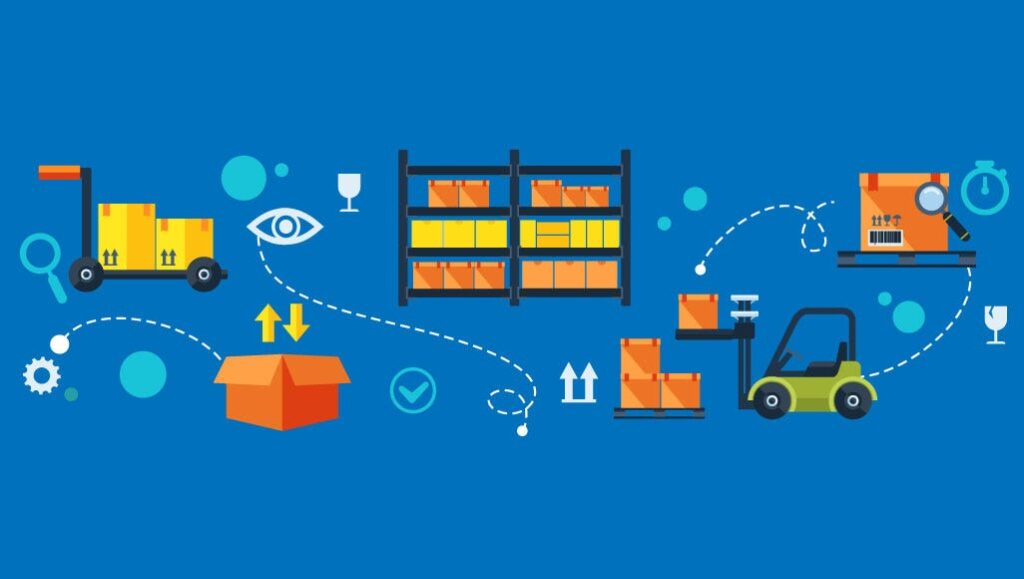
Over the years, the role of the Materials function has significantly evolved from being a mere gatekeeper to becoming a strategic partner in joint ventures (JVs) and long-lasting buyer-supplier relationships. This evolution has transformed the Materials function into a profit center, contributing to the expansion of the bottom line by achieving shorter throughput times.
Working capital management is a critical aspect for a Materials executive, who must balance the constraints of working capital with the need for a continuous flow of materials to avoid production delays. The Materials executive has seen their role grow from traditional purchasing to include material and supplier management, as well as working capital control, a vital responsibility since they oversee approximately 65% of the company’s working capital.
This program aims to help you grasp the significance of inventory management through various performance indicators. Understanding these indicators will shed light on the importance of maintaining an agile and lean organization, while also ensuring consistent production levels.
In today’s economic climate, managing inventory is more crucial than ever. With economic activity slowing, decisions that result in excess inventory can have long-lasting impacts, and the working capital tied up in inventory becomes even more problematic when capital is scarce. This program will guide you in improving inventory positions, lowering operating costs, and enhancing customer satisfaction by enabling quick responses to customer demands, increasing inventory turns, and improving line-level accuracy.
This program covers the evolving role of the Materials function, transitioning from a traditional, arms-length approach to a more collaborative partnership and JV model. This evolution ultimately leads to optimized working capital management and overall cost reduction. The key areas of focus include:
- The Role and Cost of Inventory: Understanding the financial impact of inventory on the organization.
- Principles of Common Control Techniques: Fundamental strategies for managing and controlling inventory.
- Practical Pitfalls and How to Avoid Them: Identifying and avoiding common mistakes in inventory management.
- Relationships Between Stock Levels, Ordering Frequency, and Customer Service: Balancing inventory levels with the need for timely ordering and maintaining high levels of customer service.
- Focusing Efforts Effectively: Prioritizing efforts in areas that will yield the most significant impact.
- Choosing Cost-Effective Control Methods: Selecting the most efficient methods for inventory control.
- Calculating Control Parameters: Determining key metrics for effective inventory management.
- Forecasting Stock Levels, Values, and Holding Costs: Predicting inventory needs and costs to optimize stock levels.
- Implementing Effective Monitoring and Exception Reporting: Establishing systems to track inventory and identify issues promptly.
- Different Methods & Models of Replenishment:
- Re-order Point: Setting optimal re-order levels.
- Routine Review: Regularly assessing inventory levels.
- Impact of Demand Inequities: Managing fluctuations in demand.
- Demand Management: Aligning inventory with demand patterns.
- Materials Requirements Planning (MRP): Planning for material needs based on production schedules.
- Kanban Systems: Using visual signals to trigger replenishment.
- Consignment Stocks: Managing vendor-owned inventory at your site.
- Inventory Control and Management: Comprehensive strategies for overseeing and managing inventory effectively.
- The Review Cycle: Regularly evaluating inventory practices to ensure ongoing effectiveness.
This program will equip you with the tools and knowledge to navigate the complexities of modern inventory management, ensuring your organization remains lean, responsive, and cost-effective.